Power industry needs:
State Grid proposes to build an“ubiquitous power Internet of Things”, centering on all aspects of the power system, fully applying modern information technology and advanced communication technology to realize the interconnection of all aspects of the power system, with comprehensive status awareness, efficient information processing, and convenient and flexible features Smart service system. One of the key construction directions is to fully promote the physical ID around the core value chain of the entire life of the power asset, realize the information link of all links in design, procurement, construction, operation, and decommissioning, realize the interconnection of materials and supplies in the entire process of supply and demand of materials, and the entire process of business online Integrate and share all aspects of asset detection and operation defect information to improve equipment quality and material operation capabilities from the source.
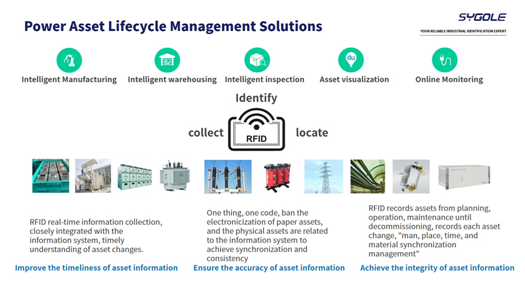
Sygole solution:
Sygole has formed a complete set of system solutions based on PFID intelligent sensing technology from product manufacturing, warehouse management, equipment inspection, asset positioning, and online monitoring. Through the close integration of RFID real-time information collection and information systems, timely understanding of asset changes and improving the timeliness of asset information; "one thing, one code" bans the electronicization of paper assets, realizing the correlation and synchronization of asset assets and information systems to ensure accurate asset information RFID tags record every change of assets from planning, operation, maintenance until retirement, to achieve "people, land, time, things" synchronous management, to achieve the integrity of asset information.
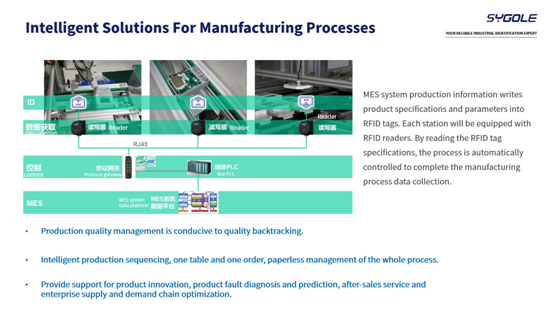
Application link:
Smart manufacturing:
² Industry characteristics: Most power equipments have complex structures and unstable demands. At the same time, they often need to be specially designed and produced according to the specific needs of users. This requires production lines to be more transparent, controllable, and more efficient.
² Customer pain points: The quality data and problems in the manufacturing process cannot be quickly and accurately traced, the production sequencing is time-consuming and laborious, and consumes a lot of paper forms.
² Solution: Write product specifications and parameters to RFID tags through MES system production information, install RFID readers at each station, and automatically control the process by reading RFID tag specifications to complete the manufacturing process data collection.
² Value benefits: Optimize production quality management, which is conducive to quality traceability; realize intelligent production sequencing, one table and one order, and paperless management of the entire process; provide support for product innovation, product fault diagnosis and prediction, after-sales service, and enterprise supply and demand chain optimization.
Intelligent warehousing
² Industry characteristics: Traditional power storage management operations include: receiving, putting on shelves, replenishing, picking, packaging, and shipping. In the current competitive environment, enterprises must constantly improve to meet the needs of supply chain competition and further strengthen materials Intensive management, improve the efficiency of material distribution, reasonably control inventory, and reduce logistics costs.
² Customer pain points: huge amount of labor, time-consuming and labor-intensive logistics inefficiency, difficulty in finding goods, inaccurate location information, and high requirements for employees' sense of responsibility.
² Solution: Through AGF automatic unloading, unmanned operation of planned paths, forklift RFID intelligent transformation, automatic identification of goods, intelligent handling and unloading; through the installation of RFID readers or intelligent access doors at the entrance and exit to achieve high-speed batch storage identification; Set up warehouse system, or RFID intelligent transformation of warehouse and equipment to realize warehouse transparency and efficient inventory.
² Value gains: Realize energy-saving, efficiency improvement, real-time transparency and intelligent handling of power asset warehousing and logistics management.
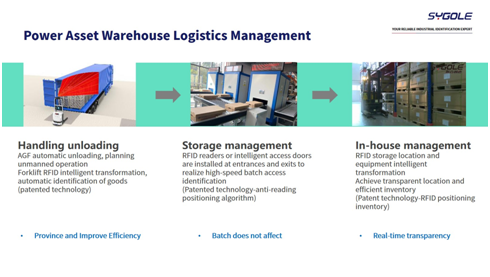
Intelligent inspection
² Industry characteristics: In order to ensure safe production, regular inspection and rapid maintenance of power equipment are required, but it is currently recorded in manual operation (some adopt one-dimensional barcodes, easy to deface, and difficult to read), sorting and summarizing, resulting in time Long, low efficiency and high error rate.
² Customer pain points: Due to the lack of effective supervision measures, the seriousness of the inspection work is often only based on the consciousness of the employees, which brings considerable difficulty to the evaluation and assessment of the inspection personnel, and the staff manually records the inspection items. Convenient, not easy to save and handle.
² Solution: Independent design and development of a media-independent label, the label shows the same super performance under any media: 20 meters in the experimental environment, PDA-8 meters in actual working conditions, and 14 meters in the fixed reader Carry out preliminary monitoring when the inspection label is installed, and write the inspection result and geographic location into the label through the handheld machine, which is convenient for information tracing.
² Value benefit: Real-time transmission of data to improve the efficiency of patrol inspection; "one object and one code", automatic warning of patrol inspection; quantitative and standardized management of patrol inspection tasks.
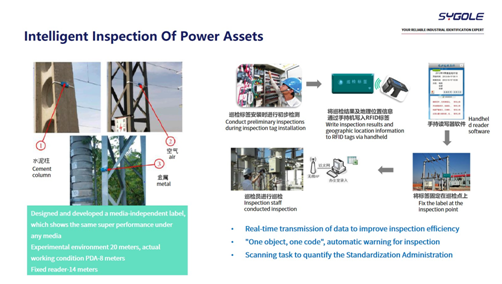
Asset visualization
² Industry characteristics: The large number of power assets, wide distribution, many specifications and models, frequent changes, fast technology updates, and large amounts of money are easy to cause equipment idle or even lost or repeated purchases, resulting in low utilization rates and increased operating costs.
² Customer pain points: The physical information and management information system information cannot be synchronized in real time, and the current actual location and status of the asset (idle, normal use, maintenance, scrap) cannot be understood in real time.
² Solution: Bind each asset in real time to view the location of the asset through the RFID tag. When the asset moves, it will record the time and trajectory of the asset movement, and the asset information can be obtained from the tag report data.
² Value benefit: Real-time dynamic management and control of power assets, helping equipment asset failures to be repaired with one click, reducing asset losses and improving work efficiency.
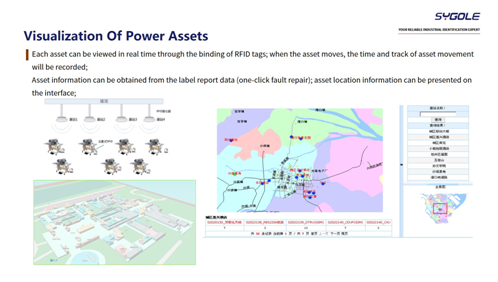
Online Monitoring
² Features of the industry: Ontology and transition information of power transmission and transformation equipment are difficult to collect in time and accurately, and the life cycle of equipment is long. Enterprise planning and decision-making lack scientific, accurate and effective information basis.。
² Customer pain points: The monitoring of power transmission and transformation equipment is done manually offline, and the acquisition of transient information such as ontology attributes and inspections is inefficient.
² Solution: Provide a smart grid equipment detection system based on RFID technology Internet of things data fusion technology, realize the perception and collection of online monitoring information of power transmission and transformation equipment through smart sensors, and collect the status information of equipment body attributes and inspections through RFID.
² Value benefit: Realize fast and efficient real-time data collection of power transmission and transformation equipment, which can provide scientific accurate and effective information basis for enterprise planning decision.
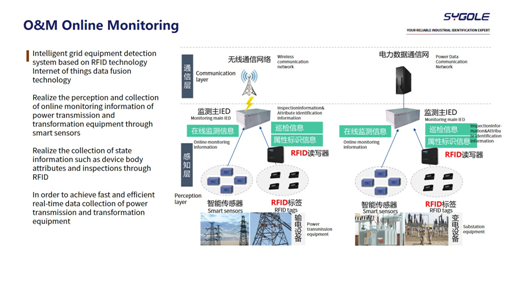