Automotive industry needs:
The automotive industry is currently one of the manufacturing industries with the highest concentration of automation, but the current automotive industry product form and production methods are undergoing rapid changes, and the production methods are evolving into flexible, digital, automated, and data-based intelligent manufacturing systems. Personalized, large-scale customized production is becoming a trend. However, traditional manufacturing in the automotive industry has problems with complex processes, high quality risks, high labor costs, waste of resources, and opaque data in terms of production, distribution, logistics, asset management, etc., and urgently needs to be solved through intelligent technologies and solutions.
Sygole Intelligent Logistics Solution:
sygole has formed a complete system solution from the four major processes of the entire vehicle to the powertrain machine assembly, from parts distribution to the production line sorting and distribution, from the off-line of the commercial vehicle to the delivery of the warehouse, in order to achieve the elimination of intermediate links , The effect of saving people to improve efficiency and transparent management. The solutions provided by sygole are helping automobile manufacturing enterprises realize the transformation of transportation and unloading, material storage, warehouse management, picking and delivery, intelligent manufacturing traceability, etc., and they are used in many automobile, power and spare parts factories of many leading automobile companies. Successfully applied.
Application link:
1 Intelligent transportation and unloading:
² Industry characteristics: There are many types of parts and components and a large number of suppliers in the automobile manufacturing enterprises. There are laborious communication requirements, large inventory of materials, congestion of logistics vehicles in the factory area, unbalanced unloading scheduling, and urgent shortage of materials.
² Customer pain points: congestion in and out of the pile, disorderly use of resources, and alarms for material shortages.
² Solution: Through the application of RFID, visual and other perceptive products + logistics vehicle management software + laser navigation unmanned forklift, intelligent management of logistics vehicle guidance and unloading is realized.
² Value benefit: Realize vehicle intelligent guidance, real-time allocation of cargo space, real-time monitoring of occupancy status, warehouse congestion rate is reduced by 70%, unloading resource utilization is increased by 100%, personnel is reduced by 30%, and abnormal working hours are lost by 90%.
2 Intelligent storage of materials:
² Industry characteristics: The supply chain management of automobile manufacturing enterprises is cumbersome and complicated. At present, lean, less labor and efficient intelligent management have not yet been achieved. There are generally reduced labor costs, logistics tracking management of materials and vehicles, and the information of materials entering and leaving the warehouse is automatic and fast Collection and other needs.
² Customer pain points: chaotic bills, low storage efficiency, and many staff.
² Solution: By installing RFID intelligent access door at the warehouse, instead of manual code scanning, automatic high-speed batch reading can be achieved. The speed is up to 11km / h, and it can support up to 150 simultaneous identifications. The reading rate is> 99.99%, leading the unique Some patented algorithm technology is the first to realize anti-reading function.
² Value gain: Realize the rapid entry and exit of bulk goods, save people and improve efficiency; automatic upload of data to WMS, transparent management; batch goods inspection function, foolproof and error-proof; single door + 4 AGVs save 3-4 people, single vehicle The unit profit is 10.8 yuan.
3 Intelligent management in the library:
² Industry characteristics: With the expansion of the scale of automobile manufacturing enterprises, the growth of varieties and production capacity, the supply of materials has increased dramatically, the management of materials, distribution time, capital, and personnel have been huge. The management in the warehouse has become a multi-variety, high-volume, high-output The key path for enterprise cost reduction and efficiency improvement.
² Customer pain points: Inconsistent charge items, difficult inventory, opaque location information, and large staff.
² Solution: Ground storage location: through AGV RFID transformation, realize the binding of cargo label and storage location label information; high-position storage location: RFID transformation through forklift, cooperate with intelligent shelf, realize the binding of cargo label and storage location label information.
² Value income: the goods are automatically loaded into the cargo space, saving people to improve efficiency; data is automatically uploaded to WMS, transparent management, real-time inventory.
4 Intelligent picking and outbound:
² Industry characteristics: In the sorting and distribution logistics model of traditional automobile manufacturing enterprises, material sorting is mainly manual, lack of intelligent error-making methods, and the process is complicated and error-prone; and in the material distribution link, a large amount of logistics resources are consumed and manual management The phenomenon of high cost and low efficiency is more serious.
² Customer pain points: many different parts, high quality risk, long staff training time, and low picking efficiency.
² Solution: Through RFID tag + PTL shelf + AGV, and docking with enterprise WMS, MES system, realize storage material picking, lighting guidance, pulling material guidance.
² Value benefit: Improve the efficiency of warehousing and line-side picking materials, reduce the error rate of picking, and reduce labor costs; JIT timely logistics and produce the necessary products at the necessary time.
5 Manufacturing traceability intelligence:
² Industry characteristics: Existing production lines of automobile manufacturing companies frequently print and post configuration orders, and information is limited, failing to maximize the role of MES and other information systems, and production, quality equipment, energy and other information lag.
² Customer pain points: AVI system has low efficiency, traditional label information has many blind spots and is prone to errors.
² Solution: Record the process, logistics, quality and equipment parameters of all links in the vehicle manufacturing through vehicle tags and fixed readers, implement the work of driving process equipment, and upload the system to form electronic documents in time.
² Value benefit: Realize the traceability of the entire process of the manufacturing process; reduce the risk of mis-installation of different parts, instant feedback on logistics assembly, quality and equipment problems; provide unlimited possibilities for subsequent data collection, equipment identification, production management, and after-sales.
Typical application cases:
The "RFID+" solution provided by Sigu has been widely used in many well-known enterprises and other OEMs, new energy automobile factories, and auto parts factories.
ü Typical Case-A
Project Background:
The original traditional production line of A Automobile Factory frequently printed and pasted the configuration list, and the information presentation was limited. It failed to maximize the role of MES and other information systems. Production, quality, equipment, energy and other information lag behind, which cannot meet the needs of many varieties and small batches of cars The flexible customized production needs urgently need to ensure the continuous, transparent and real-time data information flow of the automobile manufacturing process through intelligent perception technology to reach a new level of automation and manufacturing efficiency.
An Introduction:
sygole provides customized solutions, independently developed and produced RFID products are used in assembly lines, conveyor lines and other lines (read and write heads are installed on the station, tags are installed on the tooling board / pallet) to complete the automatic data , Real-time acquisition, to achieve automatic docking with MES system, PLC and testing equipment.
Project application:
This project has realized RFID automatic collection in more than 10 stations, and cooperated with the MES system to complete the functions of mixed flow production type change reminder and real-time operation guidance.
Value gain:
Realize traceability of the entire process of the manufacturing process, eliminate manual paste configuration work, reduce the risk of mis-installation of different parts, timely feedback on logistics assembly, quality and equipment problems, and provide unlimited possibilities for subsequent data collection, equipment identification, and production management.
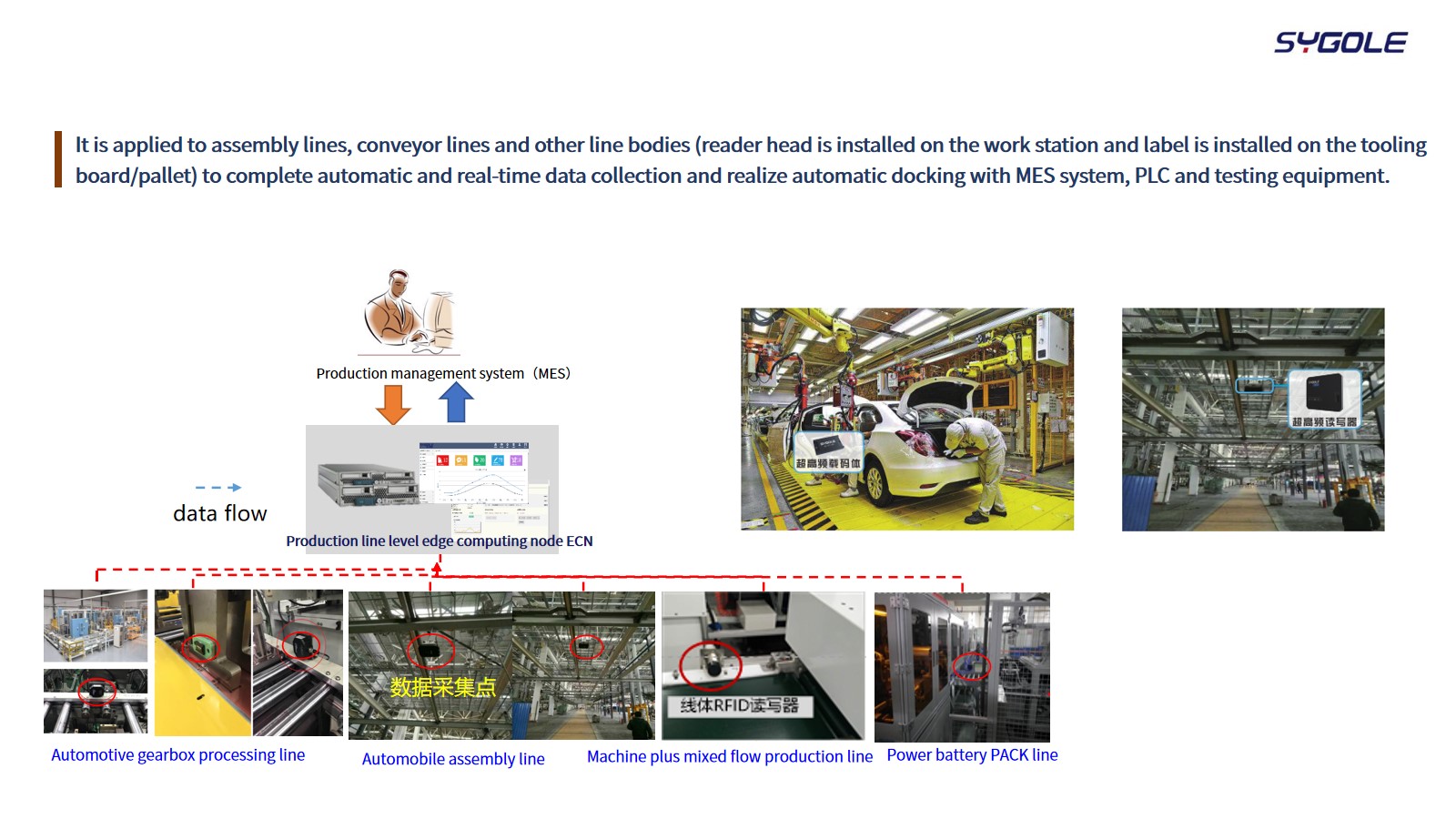
üTypical Case-B
Project Background:
The assembly parts warehouse of a plant of B mainly supplies manual materials such as barcode scanning, handling, and inventory to suppliers, resulting in time-consuming and labor-intensive, low efficiency, error-prone, and opaque location information. It is difficult to deliver goods, and it is difficult to meet the needs of intelligent factories. There is an urgent need to realize intelligent logistics for automatic batch data collection and intelligent decision-making through advanced technologies such as intelligent perception.
An Introduction:
sygole provides a customized "intelligent storage and storage + storage location management" program to realize supplier preparation, shipment, receipt, storage monitoring and logistics scheduling in the factory, to achieve storage transparency and rapid positioning of materials. The specific plan is as follows:
l A unique coded RFID electronic tag is bound to each revolving container (material rack, revolving box)
l Suppliers use RFID handsets to bind supply orders and write cargo information to RFID electronic tags
l Automatically recognize the order information and the number of warehouses through the warehouse channel door to update the inventory number of the receiving system synchronously
l Inquire the relevant bound order information on the RFID server according to the tag ID
l All data is transmitted to MES / WMS / ERP / and other information systems for calculation and processing in real time to assist decision-making
Project application:
This project uses a total of 30,000 UHF container RFID tags independently developed and produced by sygole, 16 intelligent access doors and 20 RFID smart handsets, as well as a mature warehouse management system.
Value gain:
Real-time data collection of the entire process of production and logistics in and out of the warehouse is realized, which reduces the loss of abnormal working hours caused by material shortage by 80% and reduces the cost of manual handling by 70%.
core advantages:
sygole"RFID + Intelligent Access Door" can support up to 150 sets of tags at a time, and the vehicle (forklift, AGV) pass rate can reach up to 8km / h, achieving 300W tests without missing reading, which is the industry's unique leading technology .

üTypical case-C
Project Background:
C is building a smart factory in an all-round way, and is evolving towards a flexible, digital, automated, and data-based intelligent manufacturing system to realize personalized and large-scale customized production of new energy vehicles. Among them, the unmanned integration project of stamping logistics needs to reduce the labor cost, reduce the error rate of information, provide system transparency through intelligent perception technology, create a benchmark demonstration application, and provide reference for other logistics unmanned projects.
An Introduction:
Sigu provides a customized "unmanned integration of stamping logistics" solution, through RFID technology to achieve stamping homemade parts off-line, warehousing, warehousing, wiring, and emptying, the entire process information can be traced, and the state and position of the material frame are accurate management.
l Through docking with the MES system, obtain the stamping off-line packing information and write it into the RFID system
l By docking with the EWM system, to obtain task assignment instructions, comprehensively replace manual code scanning
l Through docking with the AGV system, it is distributed to the body production line to realize the positioning and error prevention of appliances
l Manage the quantity, status and whether it is installed in the parts, and can be connected with the peripheral visualization system to achieve data sharing and real-time monitoring
Project application:
This project uses a total of 1,000 RFID tags, 2 handheld mobile terminals, 8 intelligent forklifts (renovation) and a set of RFID integrated software system.
Value Gain:
Realize warehouse information management, realize data transparency of materials, pallets, and storage location information; realize automatic identification of outgoing batches, improve work efficiency and reduce error rates; transparent storage location information, remove manual inventory and reduce operating costs.
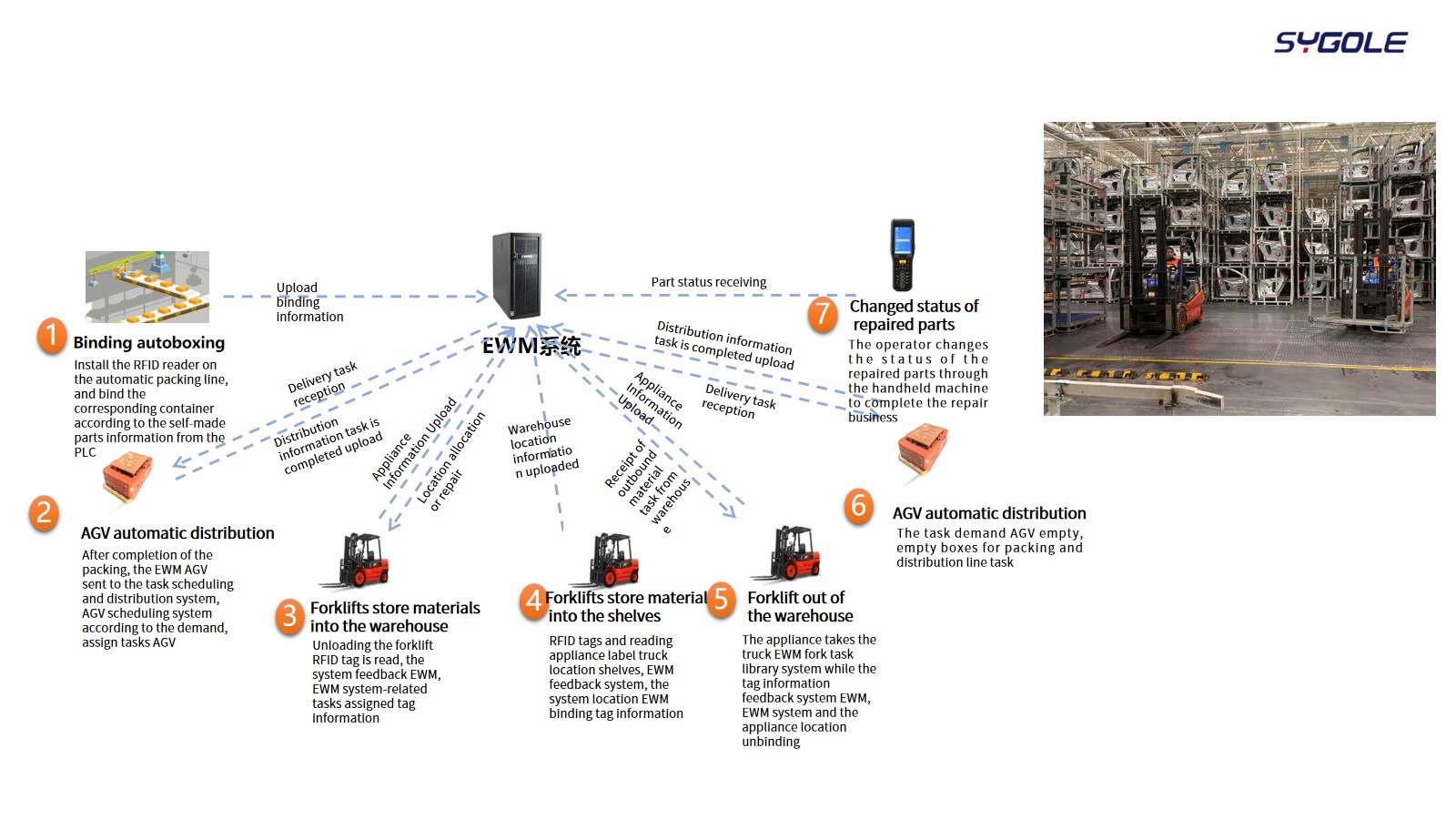
ü Typical case-D
Project Background:
D Automobile's raw material warehousing and logistics mainly rely on manual scanning, handling, inventory and other manual operations for suppliers' incoming materials, resulting in time-consuming and labor-intensive, low efficiency, error-prone, opaque location information, and difficulty in finding goods. The demand for intelligent factories urgently needs smart logistics that realizes automatic batch data collection and intelligent decision-making through advanced technologies such as intelligent perception.
An Introduction:
sygole provides a customized "intelligent storage and delivery + storage location management + intelligent picking" solution to realize supplier material preparation, delivery, receipt, storage monitoring and in-plant logistics scheduling, to achieve storage transparency and materials Quick positioning, improve the efficiency of warehousing and line-side picking materials and reduce the picking error rate and labor costs.
Project application:
This project uses more than 3000 storage RFID tags, 20,000 pallet RFID tags, 4 RFID smart forklifts, 4 RFID smart access doors, 20 RFID smart handheld machines, 16 latent AGV handling trolleys, storage Management system.
Value gain:
Realize the real-time collection of in-and-out data, improve the efficiency of forklift operations by 50%, improve the logistics distribution efficiency of sorting lines by 50%, and reduce the cost of manual handling by 70%.
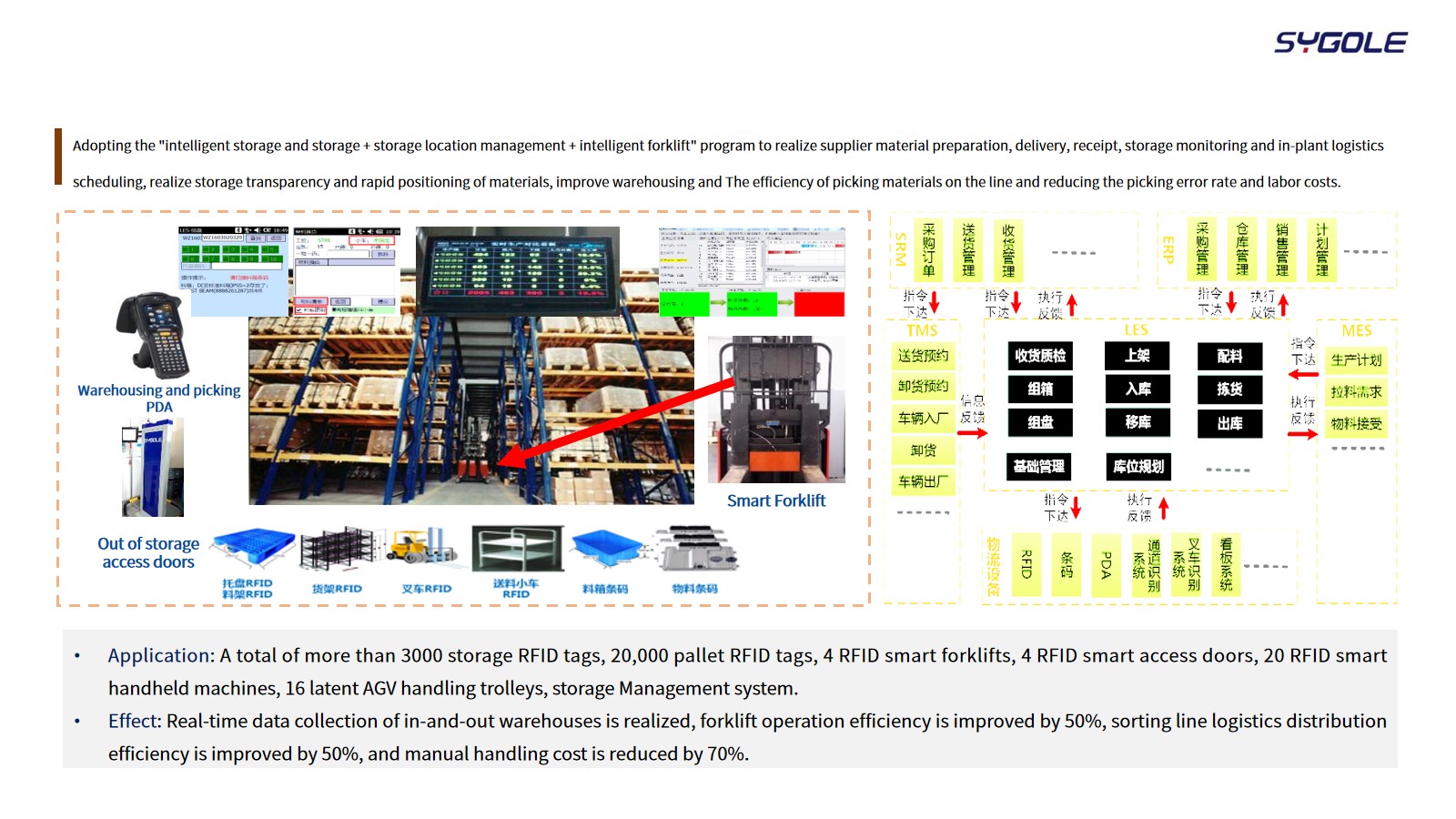
üTypical case-E
Project Background:
Most factories of E already have basic informatization software and automation hardware, but the direct connection between the software layer and the hardware layer still depends on people, and the overall level of intelligence is not high. Logistics efficiency, management level, lean inventory management and other aspects still need to be improved.
An Introduction:
sygole provides a customized "RFID-based AMP logistics" solution that realizes supply chain JIT model upgrade, finished product manufacturing and shipping process tracking, turnover container traceability, key tool life cycle monitoring and equipment intelligence.
Project application:
This project uses RFID UHF tags (anti-metal), RFID UHF handsets, RFID channel doors and other hardware products independently developed and produced, and integrates related software systems to feed back the data automatically collected by the hardware to the MES / in real time. WMS / AMP and other systems perform arithmetic processing and perform related operations according to business design.
Value gain:
Solved a series of problems such as low overall logistics efficiency, untraceable process, low utilization rate of turnover container and opaque information of E plant.
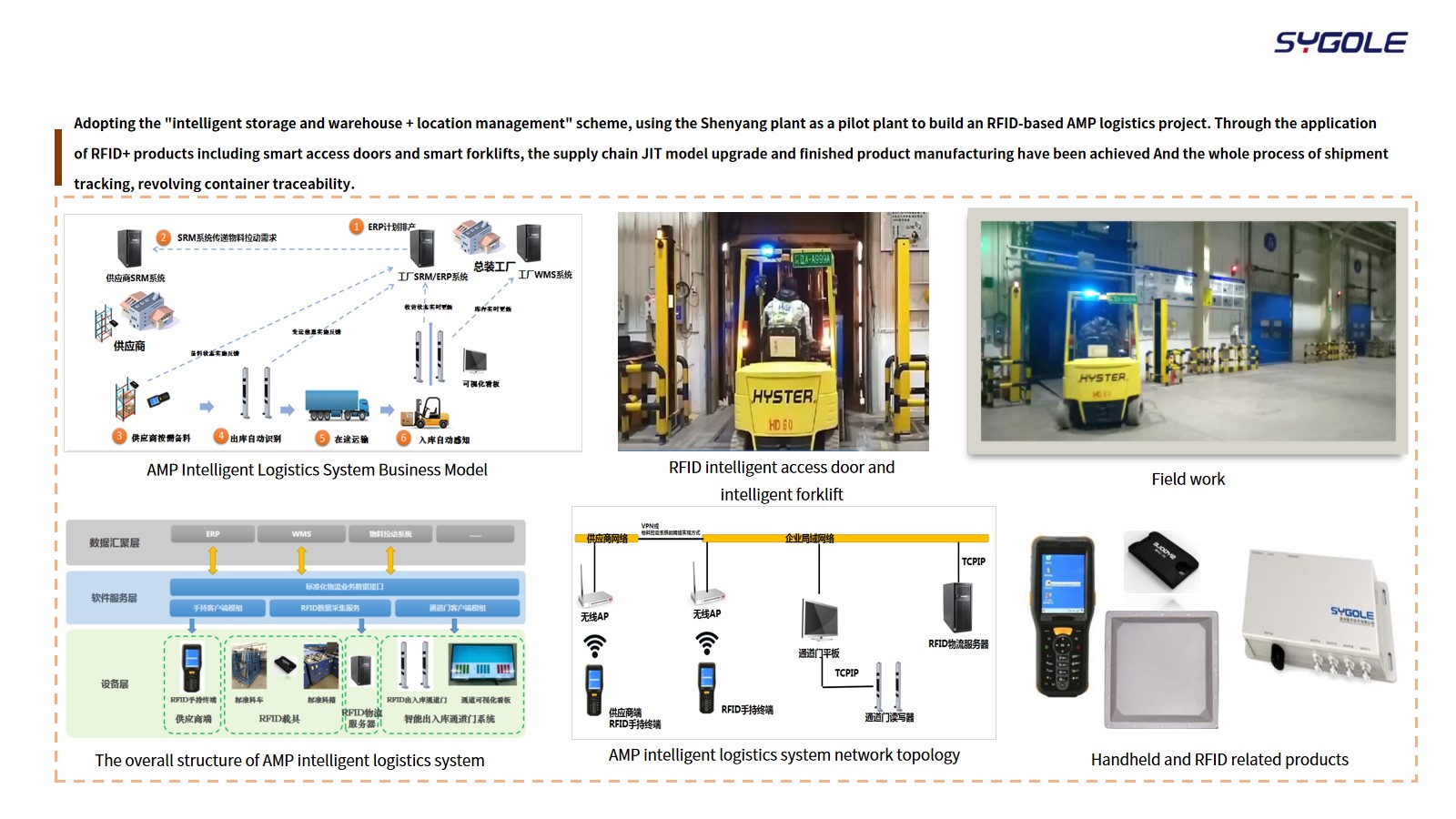
üTypical case-F
Project Background :
In the traditional logistics warehouse of a welding workshop of F, the logistics circulation action is mainly manual operation, and the logistics efficiency is low, which is difficult to meet the needs of intelligent production. At the same time, there are many kinds of equipment in the workshop, the management is difficult, and the traceability is poor. Sensing technology adds such "dumb terminals" to the digital world, enabling terminals to connect to devices and systems.
An Introduction:
The customized "intelligent warehouse solution + automatic acceptance system" provided by sygole is used in the construction project of F logistics warehouse. Automatic acceptance equipment is installed in a welding warehouse, that is, after the forklift picks up the storage parts of the warehouse and drives out of the logistics door , To achieve automatic acceptance function.
The customized "RFID material scanning system" provided by sygole is used in a welding workshop of F. It uses RFID equipment to identify the product information of the welding workshop equipment. It is fixed and connected with the two-way data of the upper layer system and AGV system, so as to realize the information traceability of the welding shop equipment products.
Project application:
A total of 2000 pallet RFID tags, 4 intelligent access doors, 7 sets of RFID readers and antennas, 2 intelligent handheld machines, and related management systems were used in this project.
Value gain:
It can realize the intelligent management and acceptance of materials in and out of the warehouse, the real-time tracking of the technical status of parts, and the transparency of inventory management; it can realize the timely collection and processing of appliance product data, and the digital management of the entire process of circulation.
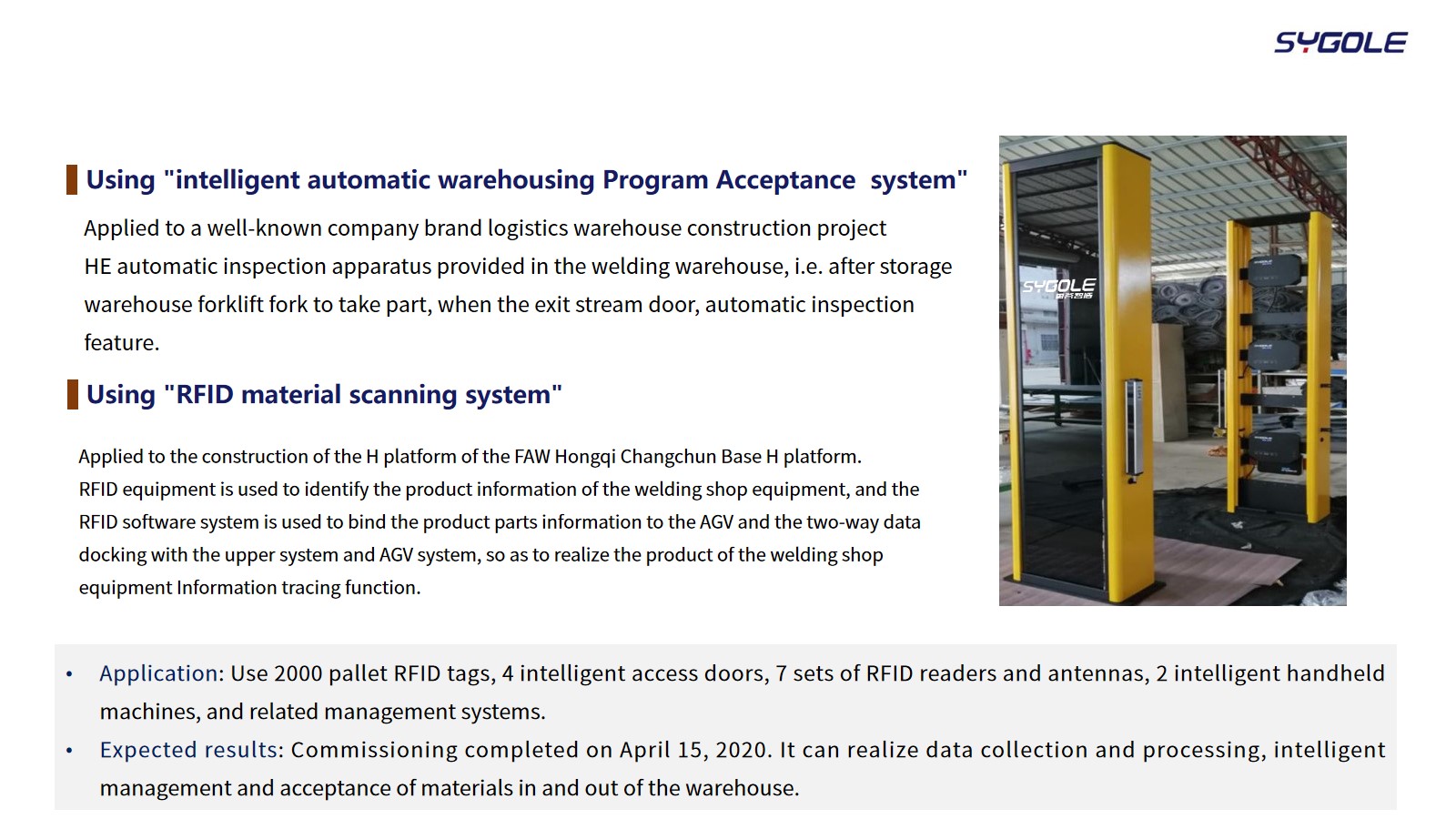